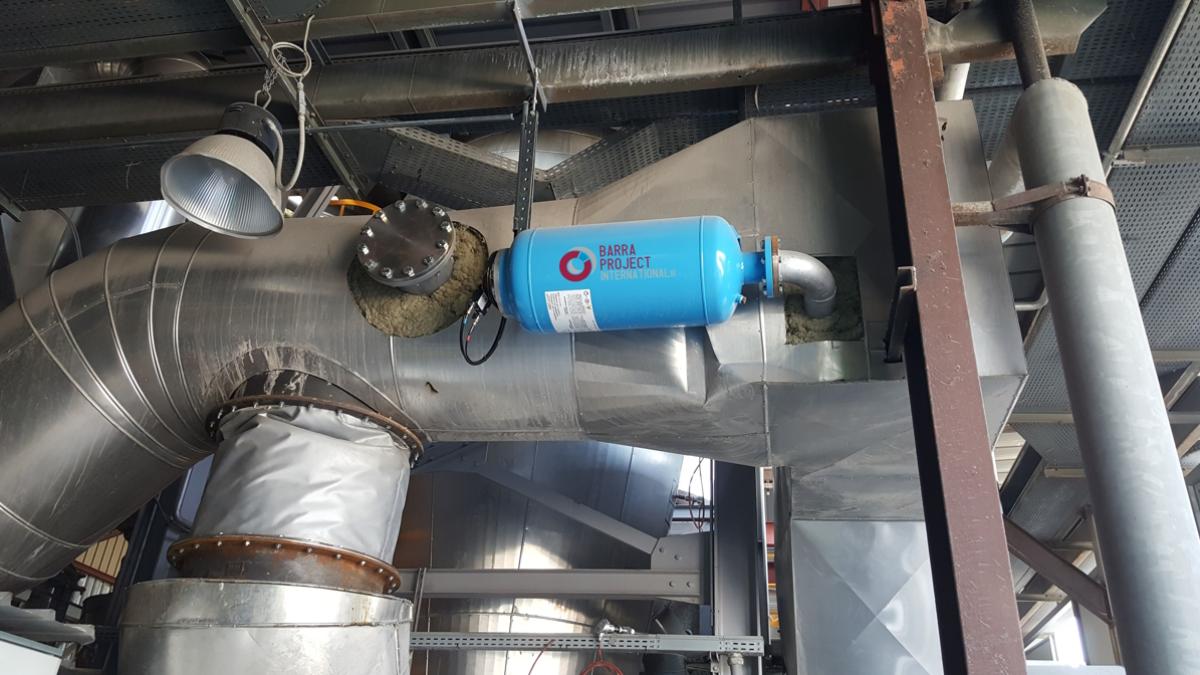
The action of AIRFLASH® is aimed at maintaining a good level of fluidisation of the stored material for extended periods of time and in the presence of unfavorable surrounding conditions such as humidity and high temperatures. The aircannon is an energy accumulator composed by an instantaneous firing valve and a tank for storing pressurized compressed air. Effective already at 2.5Bar, AIRFLASH® aircannons can work up to Pmax 10Bar.
Strengths of AIRFLASH®:
- Modular structure
- High customization level
- Longevity
- Reliability
- Efficiency
HOW DO THEY WORK?
By eliminating and preventing bridging and rat-holing phenomena, AIRFLASH® allows “first-in first-out” management of the stored material, favoring the natural emptying of silos and hoppers; by preventing the formation of bridges, encrustations, dead zones of blocked material, AIRFLASH® preserves not only the quality and good level of conservation of the ensiled material, but also the efficiency and longevity of the storage structures. The shock wave generated by AIRFLASH®, in fact, acts directly on the material unlike traditional vibration systems.
5 CASE STUDIES
Find out how AIRFLASH® has improved efficiency in the following production realities!
CASE 1
PET FOOD COMPANY - EFFECT OF SUMMER HEAT
Problem: clogged soybean silos due to sticky consistency of the stored material, due to summer temperatures. The company recorded continuous production stops due to manual unblocking of the material.
Solved with: AIRFLASH® system in the PPI variant equipped with DN100 valves combined with our EOLO diffusers for directing the shock wave inside the silo.
(PHOTO 1) AIRFLASH activation points on soybean silos
CASE 2
FLOUR & OIL MILL – MATERIAL BRIDGE FORMATION
Problem: silo clogged due to wheat flour compaction at a higher level than the extraction auger. The auger excavated the material, but at the upper level the material compacted forming a bridge which prevented its flow towards extraction. Need for continuous manual interventions to restore material flow.
Solved with: AIRFLASH® system with 30Lt LIGHT cannons and STORM activation system for the simultaneous triggering of multiple activation points. The simultaneous firing of multiple small cannons allows easy disintegration of the bridge and has a fluidifying action on the material, thus making the extraction of material from the auger fast and efficient.
(PHOTO 2) AIRFLASH LIGHT cannons above the extraction auger
CASE 3
COOKIES MILL – STRONGLY COHESIVE MATERIAL
Problem: White flour stuck in storage facility. The company intervened manually by hammering the external walls of the silo to unblock the material; when this was not enough, he intervened in extraordinary maintenance inside the silo with steel rods.
Solved with: AIRFLASH® system in the PPI variant with DN50 fire valves. Eliminated the need for direct manual interventions.
(PHOTO 3) PPI system for installation in confined spaces
CASE 4
DISTILLERY – HEAT EXCHANGER
Problem: the heat exchanger connected to the oven was losing efficiency due to deposits of dust deriving from the combustion cycle of the oven. The hot powders encrusted on the exchanger tubes with a consequent drastic reduction in the heat exchange capacity.
Solved with: AIRFLASH® system in the PPI variant with specific firing valves for application in high temperature areas. Result: the surfaces previously subject to deposits are now kept clean and the efficiency of the exchanger remains optimal for the entire duration of the production cycle
(PHOTO 4) PPI system in areas with high temperatures
CASE 5
GLASSMAKER – ENERGY RECOVERY PLANT
Problem: encrustation and deposits in the pipes of the energy recovery system for the hot dust and gases leaving the furnace. Plant inefficiency.
Solved with: AIRFLASH® system with 100Lt cannons for high temperatures with preventive cyclical activation to keep the pipes clean.
(PHOTO 5) AIRFLASH cleaning point on hot fumes duct